What is an ERP system?
✅ Why an ERP system is indispensable in production
✅ ERP systems in modern manufacturing
✅ Checklist for integration
✅ ERP system integration with the OPC Router
The ERP system
ERP means “Enterprise Resource Planning” and can be understood as “corporate resource planning”. The aim of ERP is to deploy and utilize resources in the company as efficiently as possible. An ERP system is software that supports companies in this task.
Typical business areas covered by an ERP system are production planning, manufacturing, warehouse management, human resources, purchasing and procurement, sales and customer management as well as accounting and controlling.
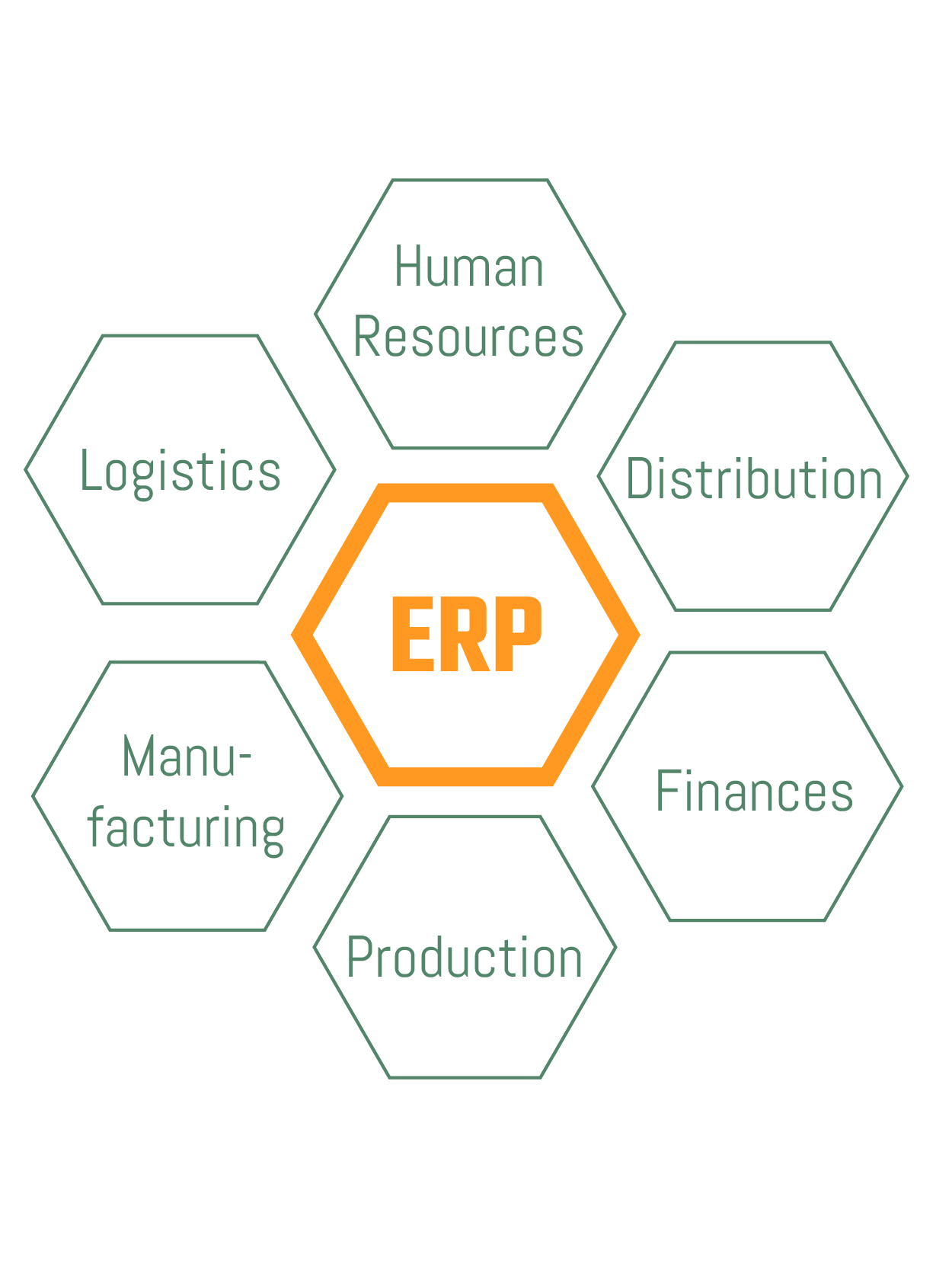
How does an ERP system work?
An ERP system is a company’s central system. Consequently, it combines all areas, processes and procedures, provides an overview of the available resources and helps to manage, plan and control them efficiently – with modern ERP systems, this is also possible in real time.
The core function of an ERP system is to link the workflows and processes in an integrated system. The basis for this is provided by centralized data management. This enables centralized data storage, improves data consistency and facilitates the flow of information between the individual areas.
Even if modern ERP systems already map a large number of workflows and processes, in practice they often also need to be linked to other applications and data sources. This is the only way to create a holistic view of all information relating to all company processes. External systems can be integrated quickly and easily via programming interfaces (APIs) and Plug-ins. One such system with an ERP/SOAP interface is the OPC Router.
Types of ERP systems
The deployment of an ERP system can be divided into three types: On-premises, cloud-based and hybrid.
On-premises:
A local ERP system is installed on the company’s own servers and computers and maintained by its own IT department. There are no monthly or annual license costs and the software can be adapted to your own needs. This option is also secure, as the data remains within the company. On the other hand, there is a high initial investment and personal responsibility for carrying out upgrades.
Cloudbasiert:
A cloud-based ERP system is a SaaS solution (Software as a Service) in which the software is located on a remote server of the provider. The provider takes over the maintenance, updating and security of the company data on behalf of the company. In addition to low investment costs, the advantages here are quick access to innovations, simple integration and better scaling options.
Hybrid:
A hybrid ERP system combines the local ERP system with a cloud-based ERP system. With this option, a company gains the flexibility to provide each application according to the company’s needs. This offers advantages, for example, for applications that have to be operated on-premises due to industry regulations or for security reasons.
ERP system connection with the OPC Router
The OPC Router is a classic middleware and supports the connection of all types of ERP systems mentioned here. Request a free, non-binding consultation on connecting an ERP system to your existing systems now:
10 advantages of an ERP system
The integration of an ERP system offers numerous advantages for your company. We support you in connecting an ERP system to your existing systems and advise you so that you too can benefit from these advantages. Contact us for a free, no-obligation consultation on connecting an ERP system with the OPC Router.
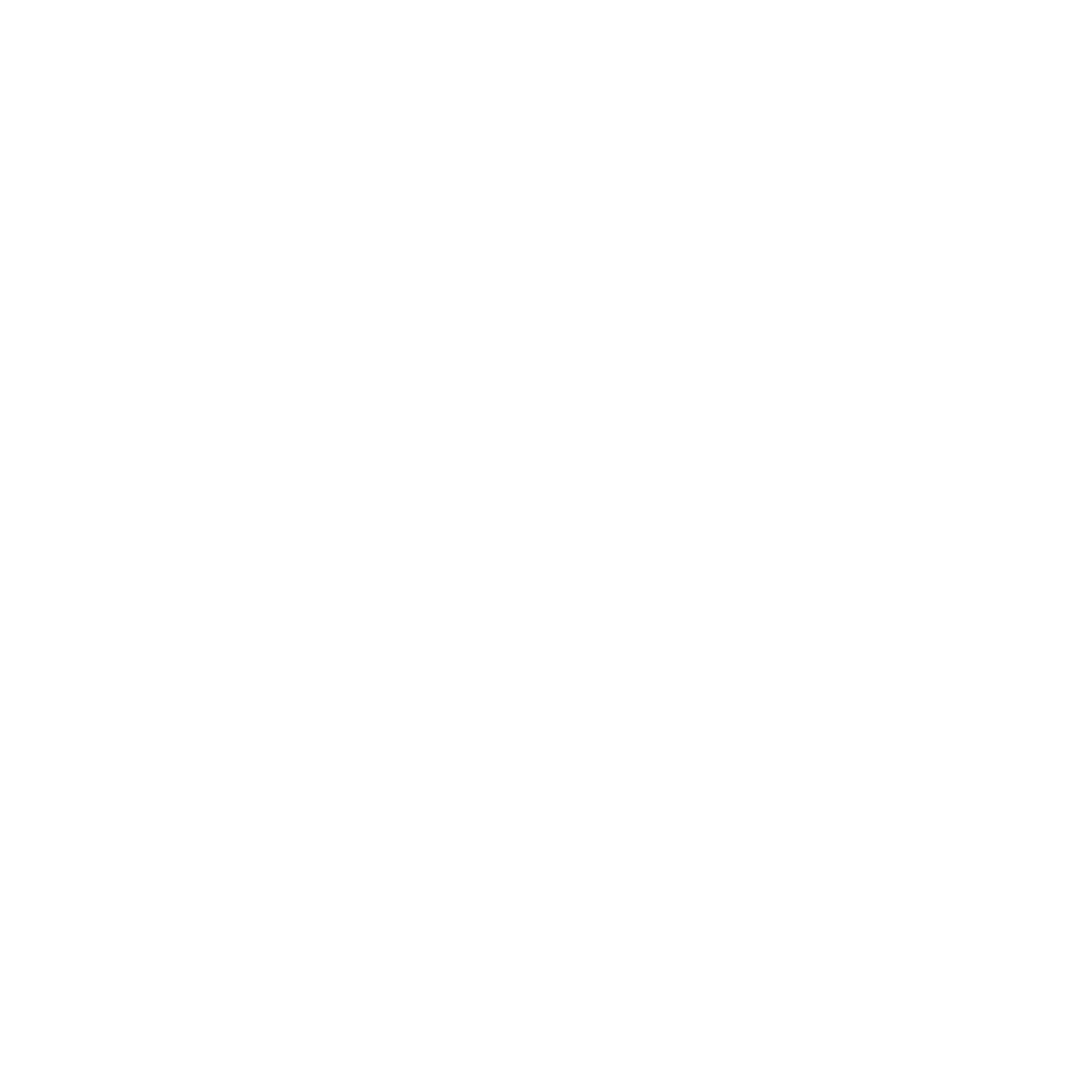
1. Centralized data management
An ERP system creates a standardized database for all departments throughout the company. This promotes a better flow of information and better communication. If the data is properly maintained or even supplied automatically from third-party systems, this is the perfect basis for properly managed order backlogs and resources.
2. Transparency
Thanks to centralized data management, all business processes are linked and displayed in one system. This means that transparent information is available throughout the company. This transparency enables cross-divisional business intelligence (BI) evaluations, among other things.
3. Process optimization
When an ERP system is being implemented, the current workflows and processes are analyzed and critically examined in order to map them in the best possible way in the new ERP system. Many ERP providers already have integrated best practice processes for this in order to make the changeover quick and easy.
4. Effectiveness
Ein ERP-System bietet eine optimale Datenstruktur. Es stellt die richtigen Daten, zur richtigen Zeit am richtigen Ort bereit und das unternehmensweit. Anwender auf egal welcher Ebene können datenbasierte Entscheidungen treffen und das auch schneller. Dies ermöglicht eine effiziente Ressourcenplanung und -Nutzung.
5. Time and cost savings
The use of an ERP system leads to a reduction in the effort required for data collection and management throughout the company. Both manual and automated processes and workflows are seamlessly integrated. Search efforts are reduced and unit labor costs and throughput times are lowered.
6. Real-time data availability
With an ERP system, all relevant data and processes are available transparently and company-wide. This allows well-founded analyses to be created and data-based decisions to be made on a daily basis. Cloud-based ERP systems often also offer the option of accessing big data information, which means that trends and developments can be identified better and faster.
7. Planning and control
An ERP system offers a transparent all-round view of all relevant resources. This enables better planning and provides better project controlling. Deviations can be quickly identified with target/actual comparisons. Thanks to integrated financial accounting, contribution margin accounting can also be called up quickly and easily.
8. Less sources of error
Thanks to centralized data maintenance, manual input and transmission errors as well as inconsistencies are avoided with the help of an ERP system. The ERP system automatically checks entered data for logical correlations and alerts the user when errors occur.
9. Scalability
ERP systems have a modular structure and can therefore be adapted to the needs and developments in the company at any time. Resources such as computer performance, the range of functions, storage space or even the required licenses can be individually adapted at any time if the number of employees increases.
10. Production planning and control
An ERP system provides a holistic view of all production planning data. This allows the departments and divisions involved to monitor and control every aspect of production planning. This integrates the entire production process, from the procurement of raw materials to the delivery of the end product.
Request your free and non-binding consultation on connecting an ERP system with the OPC Router now.
ERP in production
The basis of comprehensive ERP system integration is the networking of all systems, processes, devices and machines involved in the company.
This networking enables the production data of modern production environments to be recorded and analyzed in real time. This creates potential for optimizing production processes. This networking also creates end-to-end transparency and communication between OT (shopfloor) and IT (topfloor). This in turn increases efficiency and enables flexible adaptation to changing production requirements.
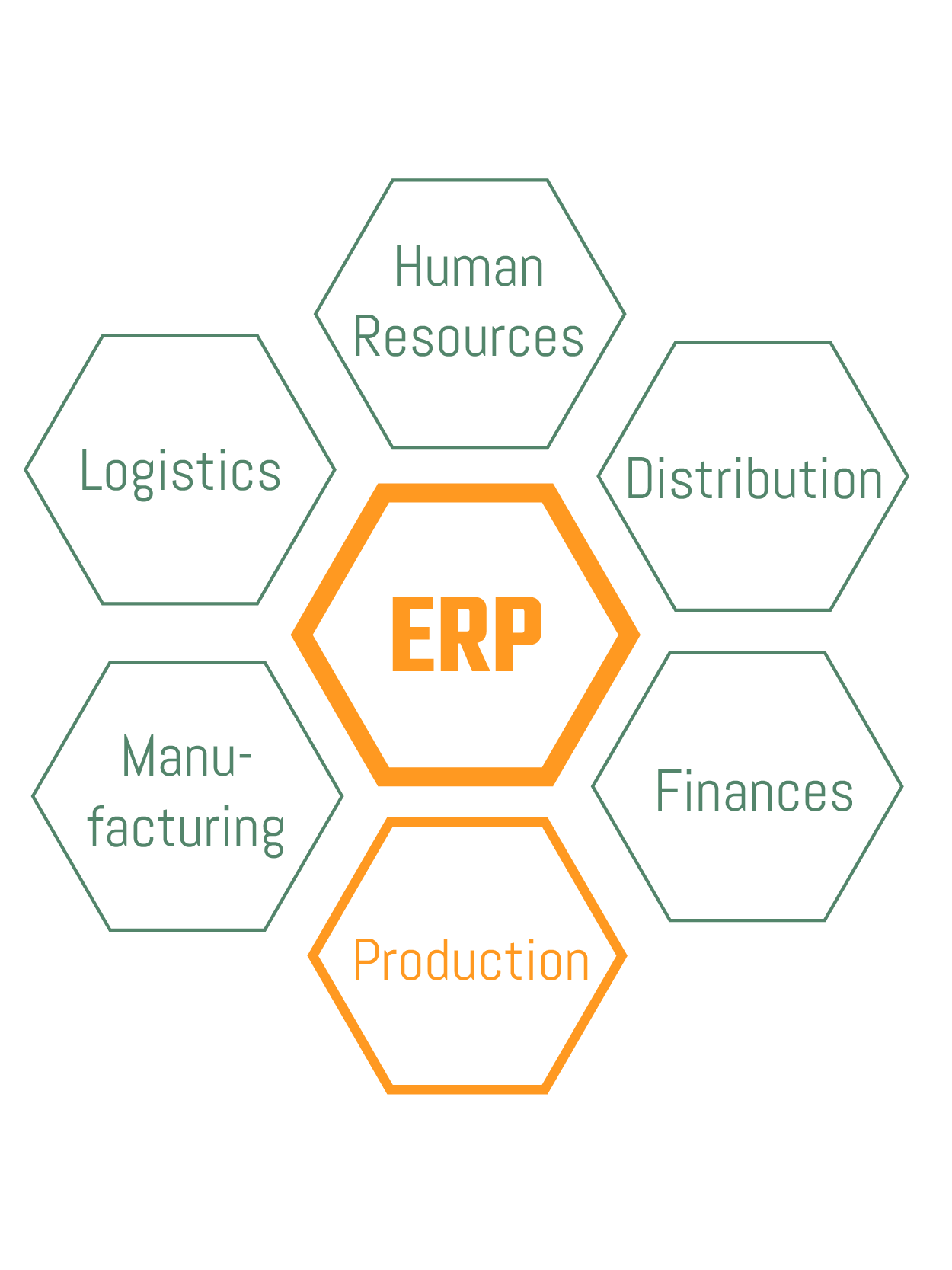
Requirements for an ERP system in production
When selecting an ERP system, functional requirements are also crucial in addition to technical requirements such as the operating system or database. These can be special requirements, such as automatic price calculation or the maintenance and updating of recipes. It is also necessary to clarify how flexible the system should be in order to be able to adapt to future changes in the company. For some companies, the provider and their previous experience in terms of industry knowledge, language or available references will also be decisive.
Industry-specific differences also play an important role. For example, the requirements placed on an ERP system in food production are completely different to those in the automotive industry. As a helpful decision-making criterion, it is advisable to obtain detailed references from the respective provider or to check whether the solution offered can be customized.
Key requirements in production
The manufacturing industry is characterized by one requirement in particular: The ability to connect all systems, machines and equipment involved in production to the ERP system. In addition, the flexibility of the system also plays an important role in fluctuating production conditions, so that the processes run optimally even then. However, every ERP system for use in manufacturing companies should fulfill these three core requirements:
Production planning and control:
Production planning supports the company in planning, controlling and monitoring production processes. It helps to create production plans, manage resources and monitor production performance in real time.
Quality management:
Quality management documents tests and supports quality improvement measures. It is important for monitoring quality standards and ensuring compliance with product specifications.
Maintenance planning:
For a company, maintenance planning means that maintenance work can be planned and carried out efficiently. As a result, downtimes are reduced and the service life of machines and systems is extended.
Integration challenges
When integrating an ERP system into an existing production environment, companies should consider three main challenges:
- Merging heterogeneous system landscapes: In many companies, there are often many different, sometimes specialized software solutions and legacy systems that need to be harmonized with each other. This requires extensive interface solutions.
- Adaptation of the ERP system to individual company processes: Standard solutions often have to be adapted or expanded to meet individual company requirements and not affect existing processes.
- Data migration and integration: Existing data from various systems must be consolidated, cleansed and transferred to the new system. Special care must be taken to avoid data loss or inconsistencies. Strategic planning, the use of experienced project teams and accompanying training can help to overcome these challenges.
Checklist for the integration of an ERP system
- Analyze requirements
- Check system compatibility with existing machines, equipment, systems and devices
- Evaluate modularity regarding enough flexibility and adaptability
- Cover industry-specific requirements
- Check references of the ERP provider
- Ensure compliance with IT security standards
- Test ERP system for usability
- Create a project timeline for the integration
- Plan process integration
- Set up interfaces
- Prepare data migration
- Organize trainings
- Ensure support and maintenance
- Cost control
- Success control
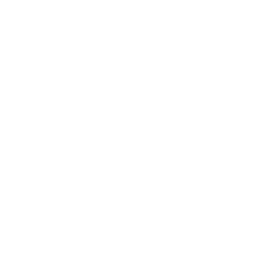
Request your free, non-binding consultation on integrating an ERP system with the OPC Router now.
Connect the ERP system with machines
The integration of ERP systems, plants, machines and other systems such as an MES system (Manufacturing Execution System) is crucial for efficient, automated production. This is the only way to enable smooth data exchange between machines, sensors, MES and ERP systems, automate and optimize processes, create transparency and achieve goals faster. Solutions such as the OPC Router, which seamlessly connect data across different levels and systems, are essential for this.
The OPC Router is a powerful platform that automates processes and offers exactly that:
- It automates data exchange from the plant via the MES to the ERP system and into the cloud.
- It supports modern and industry-relevant protocols and interfaces such as OPC UA, MQTT and REST to connect a wide variety of systems.
- In addition, the OPC Router offers connections to the most commonly used relevant industrial systems with a flexible and modular Plug-in concept.
- The ability to connect components via drag & drop saves training effort for users, as no programming knowledge is required for use.
Production orders are sent directly from the ERP system to the machines via the MES in an error-free and automated process. Production data flows back into the ERP system in real time for analysis and further use. Missing data can be retrieved easily, quickly and automatically from the connected systems.
Achieving goals with ERP system integration
These three examples clearly show the success that the integration of an ERP system with the OPC Router has led to at STIHL, HERMA and Corratec.
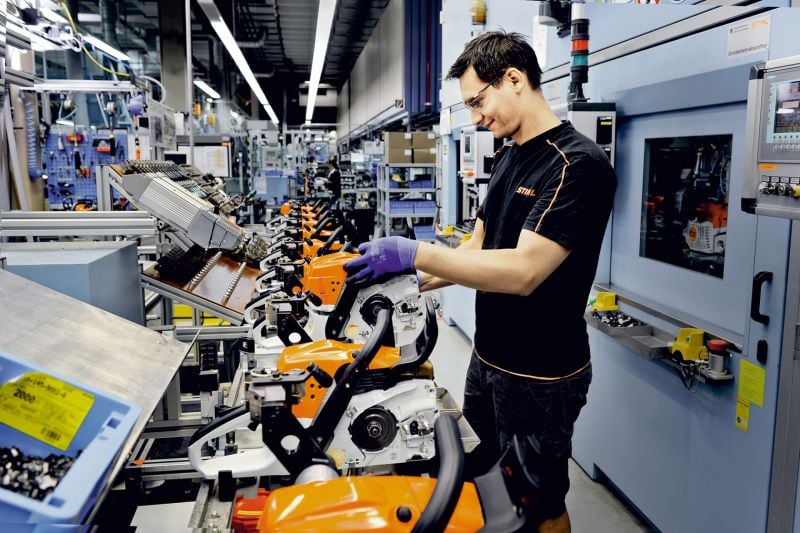
Increase automation effect
STIHL is known as a manufacturer of high-quality chainsaws, hedge trimmers and brush cutters. STIHL uses the OPC Router to seamlessly connect production facilities and the ERP system. The company increases the effectiveness of its automation through automated data transfer.
The key to modern production
The integration of ERP systems into production landscapes offers enormous advantages with optimized processes, real-time data transparency and automated workflows. At the same time, integration requires overcoming a number of challenges, such as the harmonization of heterogeneous systems and data migration. The OPC Router plays a key role in this by acting as a bridge between the ERP system, MES and production plants to create a seamless connection. Thanks to its flexible configuration and support for the latest protocols and interfaces, it offers a future-proof solution for the manufacturing industry.
Contact us to find out more about how the OPC Router can make your production more efficient and optimally network it with an ERP system:
Integrating the ERP system with the OPC Router
The OPC Router makes it easy to integrate your ERP system into your existing system landscape. Request a free demo version of the OPC Router today and test for yourself how the integration works.
- Connect your systems.
- Automate your processes.
- Optimize your production for Industry 4.0.
The download link gives you access to the free and fully functional test version of the OPC Router.